DE-STARCHING AND BIO-TREATMENT
We take any plain white fabric and de-starch it by soaking it in
water over night. The fabric is then bio treated with fermented
lemon, soda ash, reetha, amla, aloe vera and many other elements.
When the froth starts building up in the vessel, the process
of de-starching the fabric is complete. Traditionally Ajrakh
artisans de-starch the fabric with camel dung, soda ash and
castor oil. The fabric might smell foul with the traditional
method.
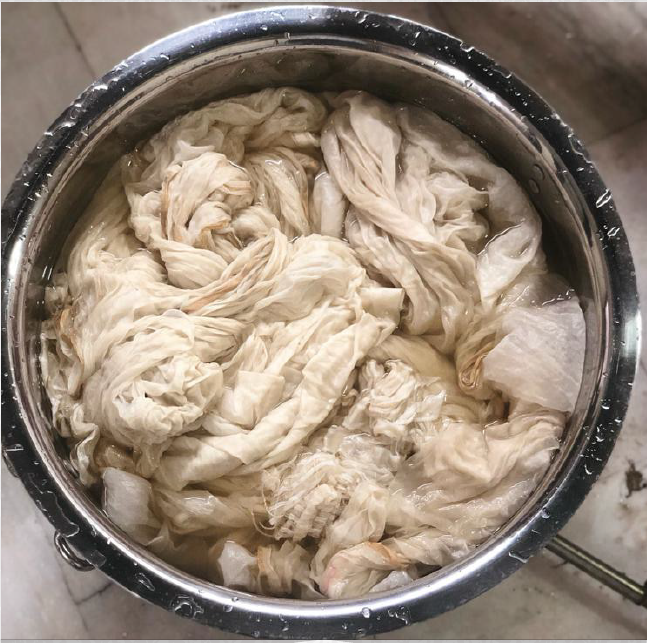
MYROBALAN WASH
The fabric is then washed with myrobalan and water. Myrobalan
is an important element in Ayurveda. It gives a yellowish cream
to the fabric and also tannic acid of myrobalan gives black
colour on reaction with iron.
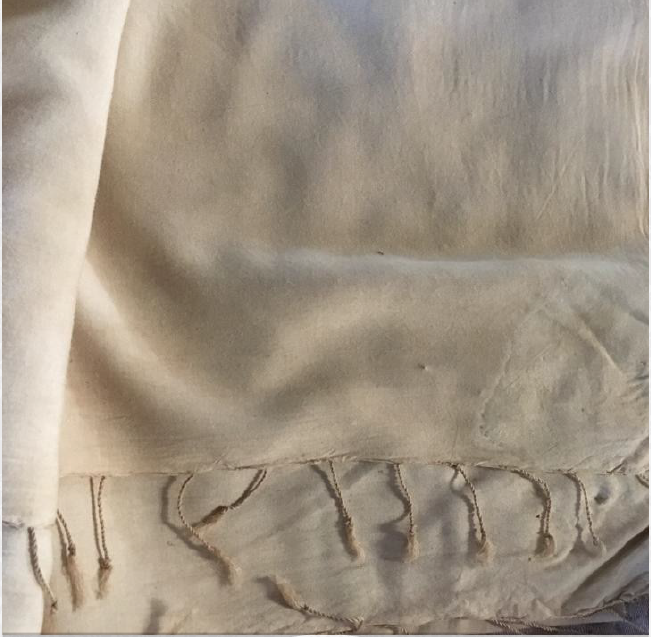
RESIST PRINTING
Then comes printing. Ajrakh uses resist print technique in printing.
Quick lime and babool resin are used to make the paste,
which will act as a shield to the fabric, when it is being dyed. The
wooden blocks are used to block print the pattern with the
resist paste. Same block is used to print the resist on both sides,
so that the fabric is not dyed on the resist patterns or designs of
the block.
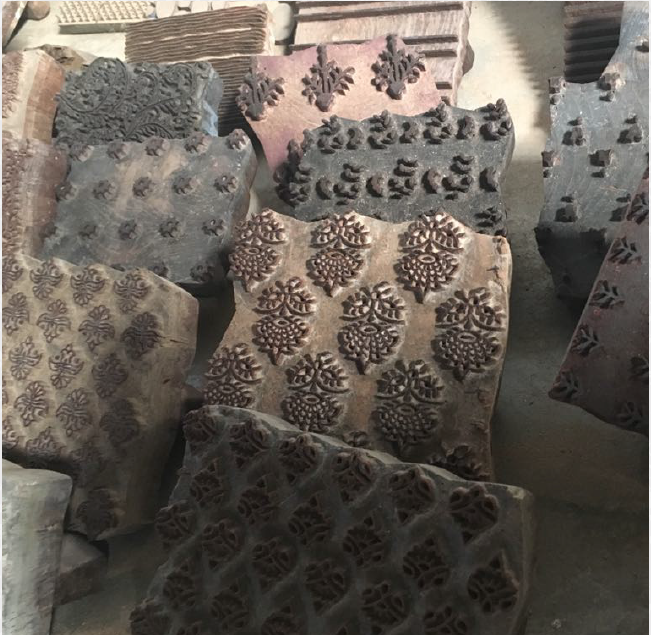
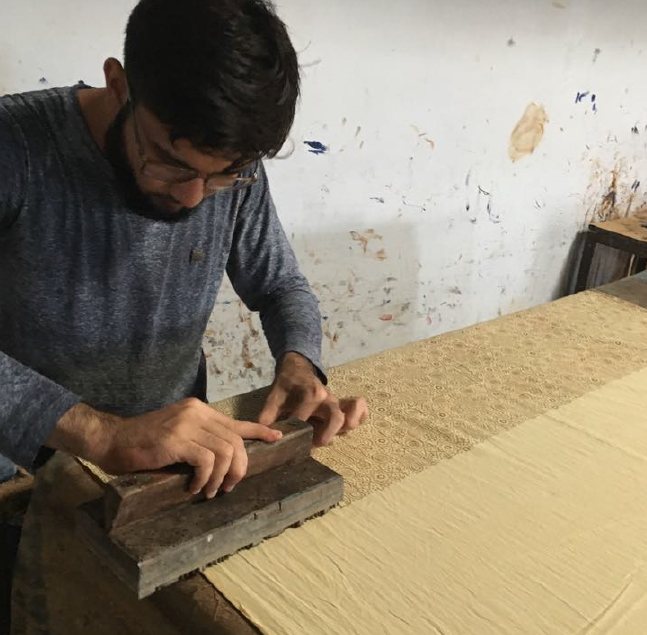
ADDING BLACK COLOUR DETAILS
To attain the black color, we go through a lengthy process. A
paste is made using rusted iron and jaggery. Jaggery speeds up
the process of iron rusting and enhances the colour. The paste
takes about 20 days to prepare. We then add tamarind seed
(kachuka) powder to this paste. The paste is now ready to be
used and is black in colour.
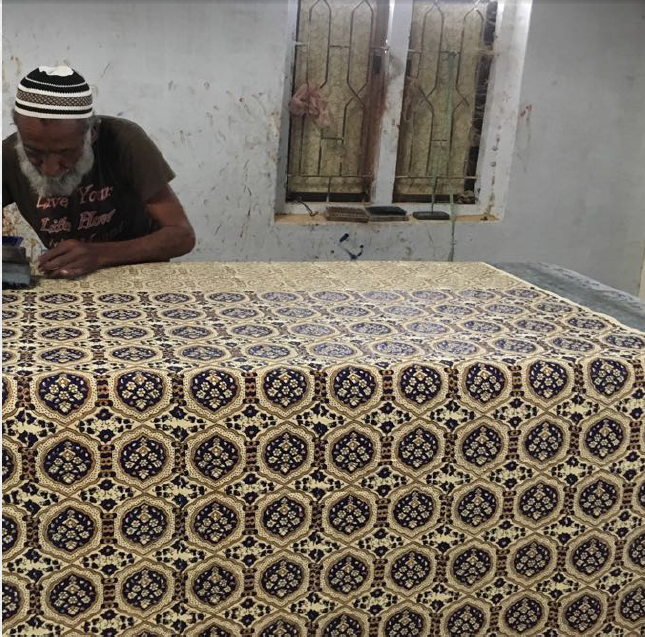
THIRD RESIST PRINTING
Now we do our third resist printing. The paste is made using
alum, clay and babool resin. The paste takes 3-4 days to be prepared.
INDIGO DYEING
The fabric is now dyed with indigo. Dyeing the fabric with indigo
once will give it a colour, but that colour will not be uniform or
consistent. It might come out patchy after the first dyeing. To
make the colour uniform and consistent, we dye it 3 times.
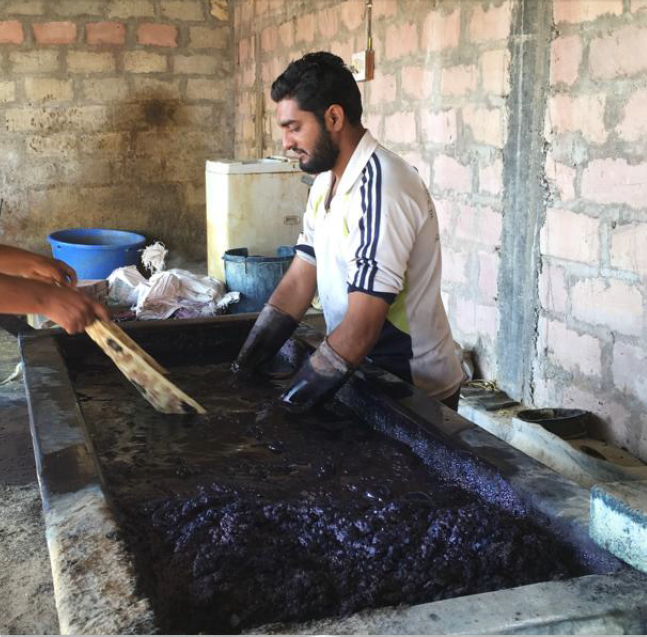
WASHING
The fabric is now washed. On washing, the resist paste will
wash off and the alum stays on the fabric. Alum’s colour
changes to yellow.
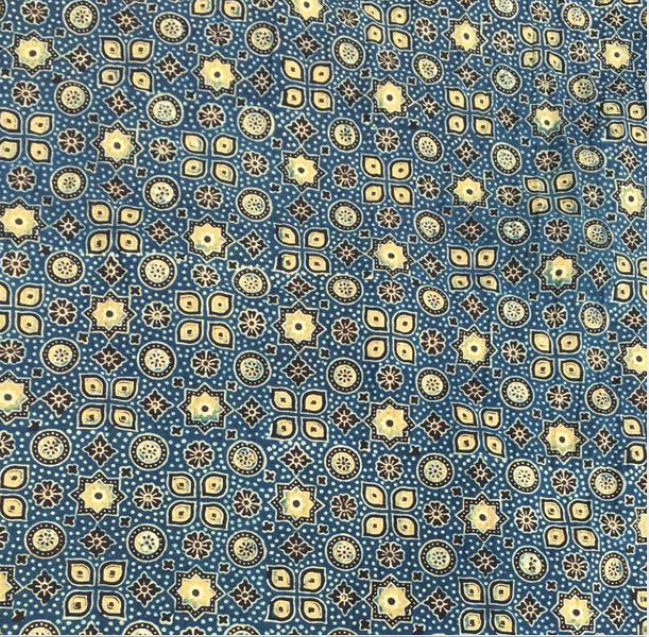
BLOCKING WITH MADDER
To complete the ajrakh print, we finally introduce red colour to
our fabric. We dye the fabric with madder, which replaces the
yellow colour of alum and changes it to a very beautiful shade
of red.
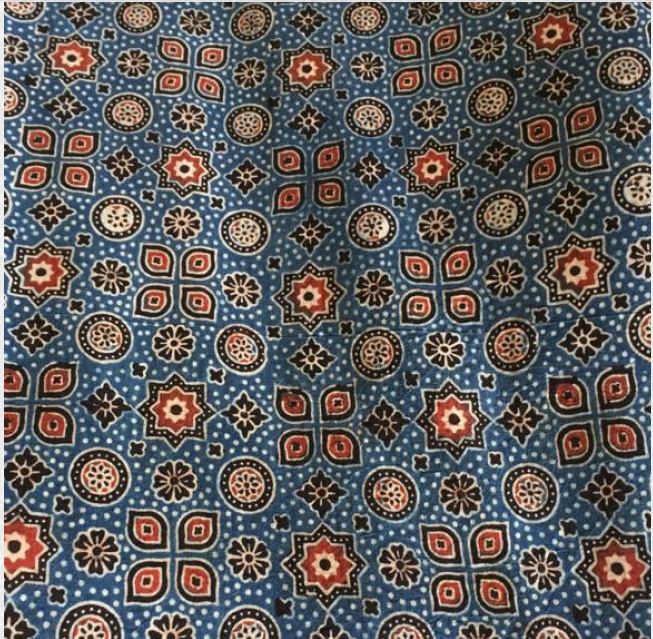
BIO-TREATMENT AND IRONING
The fabric is again bio-treated with natural elements like aloe
vera, reetha, amla, etc. Now, we iron the fabric at a very high
temperature and pressure to get rid of the wrinkles and creases.
The fabric is now ready.
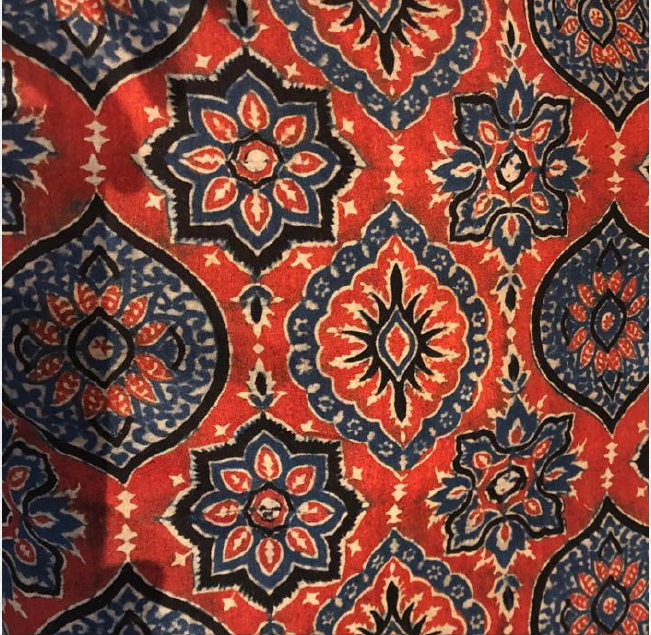
Leave a reply