History Of Bagru Printing in Bagru Town
Bagru is a small township in the district of Jaipur, Rajasthan. It is famous for its ‘signature’ in the field of block printing and natural dyes. The livelihood of the majority is artisanship. Bagru says the story of two communities, Chhipa and Raiger, who were involved in block Bagru printing and manufacturing of leather respectively.
Brief About Bagru Printing:
It is done by printing dark or coloured motifs on a cream or dyed background. the method starts by getting ready the fabric to finished written materials through their endemic strategies. Motifs having some specialty area unit transferred onto the light-weight colored background with wood blocks following 2 designs direct and resist vogue. though this method is facing issues against the threat of globalization, this exotic art of creation is needed to be inspired within the gift context of environmental consciousness.
SOAKING OVERNIGHT (Hari Sarana ,scouring):
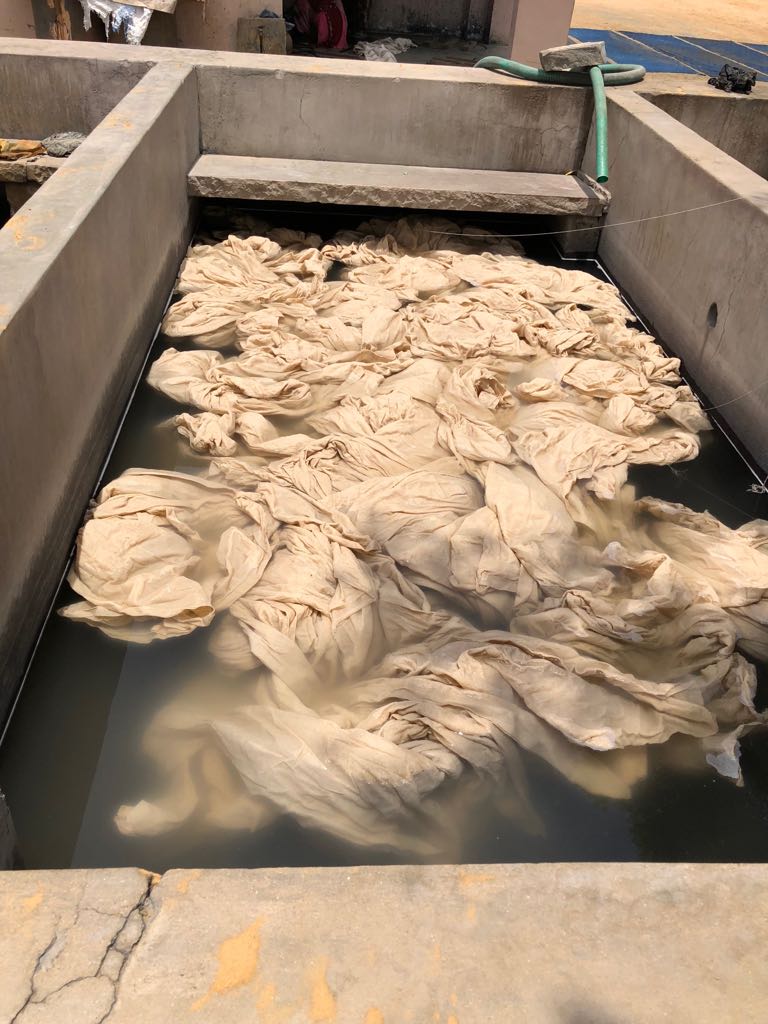
bagru printing
First, the fabric is soaked for 1-2 days. It helps to remove the stains, oil, dust, and starch which was a part in attires. This process is called ‘Hari Sarana’(scouring). Traditionally cow dung was used for this processing, but nowadays soap has replaced cow dung. And at last clothe is washed in running water after all previous process.
HARDA DYEING (‘Peela Karana’ Tannin):
When the fabric is completely contaminated free, it is treated with ‘harda’ solution which has tannic acid in it. This process Involves the use of natural mordants like Harda and Alum to capture the natural colours that we print on the fabric using our pattern blocks.
Harda is a natural ingredient which is extracted from Myrobalan fruit and has been used in the Ayurvedic medicines for its digestive healing properties. It gives a yellowish cream to the fabric and also tannic acid of harda gives black colour with ferrous. This is called ‘Peela Karana’( Tannin).
DRYING:
After Harda dyeing, the fabric needs to lay flat and dry in the sunlight . The fabric will have a yellowish tint after this stage, which will later disappear once washed.
PRINTING (Chapai):
Block printing has years of traditions to tell us. As it deals with printing in the clothes, we have a surviving example from China, 220 AD. Woodblock printing existed in Tang dynasty, China from 7th century and continues in this 21st century. However, block printing is not that common. In India, a small town in Rajasthan is famous for its block printing, Bagru.
Dabu:-
This Process involves the use of Kaali Mitti paste-a dark mud from a locality, to block print the pattern. when they dye the fabrics, the motif covered with the mud print remain uncoloured while the rest of the fabric takes on the hue of the dye.
The fabric is spread on large printing tables, where block printing will take place. The fabric is printed with the rusted horseshoe nails. This ferrous mainly use for outlining, so background block comes after and it can be printed easily. This process is also called ‘Chapai’(printing). Main colours used in Bagru are black, red and maroon. All these colours are extracted from natural sources like,
-
- Black from the worn out iron horse or camel soaked in water.
-
- Red is derived from Gum paste and phitakiree i.e alum.
- Maroon is the combination of red and black.
Apart from these, natural dyes are also used to get different patterns and designs. These are- Pomegranate, turmeric, Madder etc.
- Motifs are hand carved on wooden blocks by people who are the specialists in this.
Main Motifs used are:-
-
- Patashi- Small flowers with buds, leaves, and stems.
-
- Jhad- Intervening tendrils and distinctive borderlines.
- Hathi- Elephant.
Other designs are- flower, geometrical prints etc.
Drying (Sukhai):
After completion of printing, the fabric (printed texture) is dried for 3-4 days in order to get colors to penetrate into the fabric. This process is called sukhai(ageing) by old veterans of this art.
Washing (Dhulai):
After sukhai(ageing) is done, its time for dhulai(washing). Dried fabric is washed in running water so that extra colour should come out and does not stick to the attire.
BOILING (Ghan Ranghai):
Once dhulai has done, fabric is then boiled in a large copper pot with water, alizarin(dye) and dhawadi flowers. This is known as Ghan Ranghai(fixing of colour).
SUN BLEACHING (Tapai):
After Ghan Ranghai now it’s time for the final process known as tapai (sun bleaching). Which means the fabric is once again washed to remove excess dust and dirt. And it is kept in the sunlight for drying.
Once Tapai (sun bleaching) is done, bagru fabric is ready to use. Bagru printing cloths are used both in a modern and traditional array.
Submit your review | |





Leave a reply